Why Conduct Battery Testing?
Performance Evaluation: Battery testing is essential for assessing key performance metrics such as capacity, energy density, power density, and cycle life. These evaluations ensure the battery’s reliability in practical applications.
Safety Assurance: Testing identifies how batteries perform under extreme conditions like overcharging, short circuits, and high temperatures. This helps prevent potential safety hazards such as fires or explosions.
Quality Control: Manufacturers use battery testing to ensure each production batch meets established quality standards and specifications, enhancing product consistency and reliability.
Research and Development Support: During the development of new battery materials or technologies, testing is a critical step that aids engineers in optimizing design and material choices.
Market Competitiveness: By offering rigorously tested products, manufacturers can build market trust and enhance their brand image.
Types of Batteries
Primary Batteries (Non-rechargeable):
- Alkaline Batteries
- Lithium Batteries
- Nickel-Cadmium Batteries
Secondary Batteries (Rechargeable):
- Lithium-Ion Batteries
- Nickel-Metal Hydride Batteries
- Lead-Acid Batteries
- Sodium-Sulfur Batteries
Solid-State Batteries: These next-generation batteries use solid electrolytes, offering higher energy density and improved safety.
Fuel Cells: Generate electricity through chemical reactions, commonly used in vehicles and other transportation means.
Basic Principles of Battery Testing
The fundamental principle of battery testing involves applying various loads or charge-discharge cycles to the battery while monitoring its output characteristics (such as voltage, current, temperature). This data helps in plotting charge-discharge curves and calculating capacity along with other critical parameters.
Battery Testing Methods
Capacity Test: Measures the total energy released under specific discharge conditions until discharge termination.
Internal Resistance Test: Evaluates energy loss by measuring AC internal resistance at a specific frequency.
Cycle Life Test: Assesses battery lifespan and performance degradation through repeated charge-discharge cycles.
Temperature Impact Test: Conducts charge-discharge cycles under different temperature conditions to understand temperature effects on performance.
Rapid Charge-Discharge Test: Evaluates battery performance during high-rate charge-discharge scenarios.
Safety Tests: Include assessments under extreme conditions like short circuits, overcharging, over-discharging, and thermal runaway for safety evaluation.
Battery Test Equipment
Constant Current/Voltage Sources: Used for simulating various load conditions during charge-discharge tests on batteries.
Electronic Load Devices: Simulate different working conditions to evaluate performance.
Multi-channel Data Acquisition Systems: Monitor multiple parameters (e.g., voltage, current, temperature) in real-time and record data.
Internal Resistance Measurement Instruments: Specifically designed for measuring internal impedance.
Environmental Test Chambers: Simulate different environmental conditions (e.g., high temperature, low temperature) to assess their impact.
Analysis Software: Used for data processing and result analysis to generate reports.
Please choose BONAD for battery testing equipment. We not only provide a variety of standard testing equipment, but also provide customization.
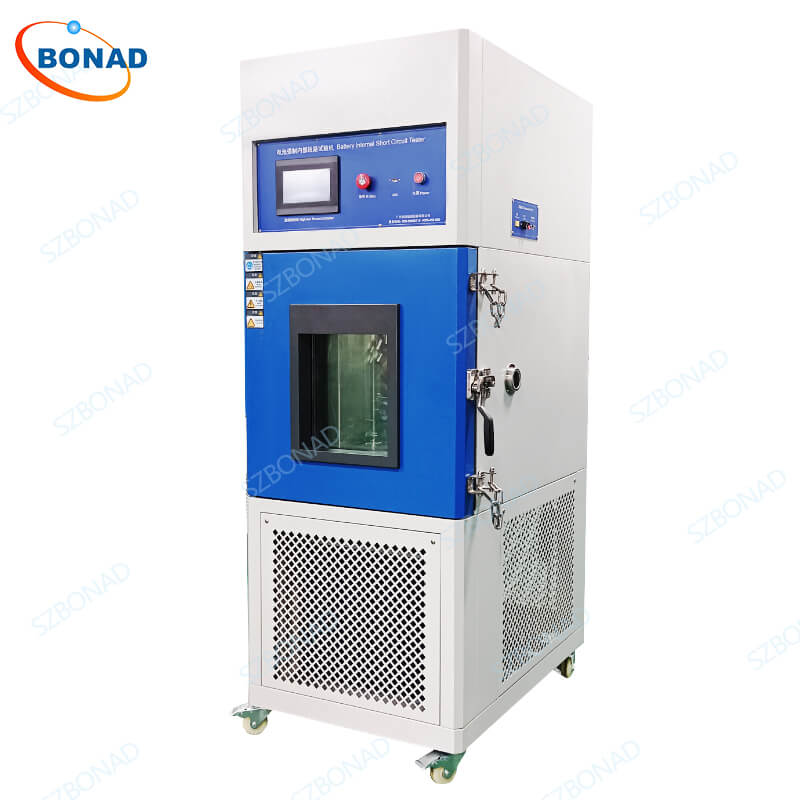
Considerations for Battery Testing
Safety First: Always follow safety protocols during testing, especially during extreme tests like short circuit or overcharging trials.
Equipment Calibration: Ensure all testing equipment is calibrated to obtain accurate data results.
Environmental Control: Maintain appropriate environmental conditions such as temperature and humidity to avoid interference with results.
Sample Preparation: Ensure samples meet standard requirements including size and condition to guarantee test consistency.
Data Recording and Analysis: Record all experimental data meticulously and conduct proper data analysis for future reference and decision-making.
Adherence to Standards: Follow relevant industry standards (such as IEC, ASTM) during testing to ensure comparability and reliability of results.