The IEC 60950 A.3 Hot Flaming Oil Test Device is a meticulously engineered tool designed to evaluate the protective performance of fireproof enclosures used in various electrical and electronic products. This device adheres strictly to Article 4.6.2 and Appendix A.3 of GB4943.1-2011 “Information Technology Equipment Safety Part 1: General Requirements.” Additionally, it aligns with the stringent standards outlined in IEC60950-1:2005. The primary application of this device lies in testing the fireproof capabilities of enclosures for products such as electronic instruments, electrical meters, information technology equipment, and other electrical devices. Ensuring that these enclosures can withstand extreme conditions is crucial for maintaining safety and compliance with international standards.
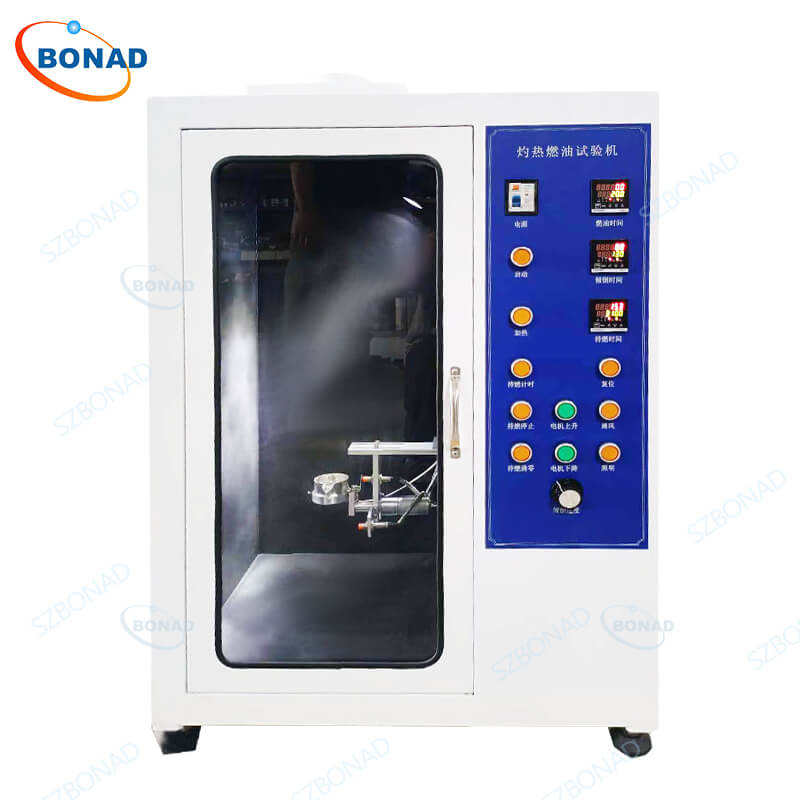
The test procedure for the Hot Flaming Oil Test Device involves a precise and controlled process. Initially, 10mL of a specified flammable liquid, characterized by an average calorific value of 38MJ/L, a unit volume mass between 0.845g/mL and 0.865g/mL, and a flash point ranging from 43.5℃ to 93.5℃, is placed into a metal spoon. This liquid is then heated to the ignition point of distillate fuel oil and burned for one minute. During this time, the spoon is rotated at a specific height of 100mm and flow rate of 1mL/s by a motor, steadily pouring the flammable liquid into the center of the sample’s opening (fireproof enclosure structure). The fireproof performance of the test product is evaluated based on whether an ignition cushion layer, positioned at a specified distance of 50mm and density of 40g/m² beneath the test product, catches fire. This rigorous testing method ensures that only the most robust and reliable enclosures pass inspection.
For manufacturers and engineers working with electrical and electronic products, the Fireproof Enclosure Testing provided by the IEC 60950 A.3 Hot Flaming Oil Test Device is indispensable. By adhering to the GB4943.1-2011 and IEC60950-1:2005 standards, this device offers unparalleled accuracy and reliability in assessing the fireproof performance of enclosures. The ability to simulate real-world fire hazards ensures that products are not only compliant with safety regulations but also capable of protecting users in critical situations. Whether you are developing new products or enhancing existing ones, integrating this testing device into your quality assurance process will significantly enhance the safety and marketability of your electrical and electronic devices.