In the ever-evolving automotive industry, ensuring that electronic components are both waterproof and dustproof has become increasingly crucial. One essential aspect of automotive electronics is the protection level testing of connector housings. A significant method for assessing their waterproof performance is through the IPX9K High-Temperature Pressure Jet Waterproof Test Chamber.
Understanding the IPX9K High-Temperature Pressure Jet Waterproof Test Chamber
The IPX9K High-Temperature Pressure Jet Waterproof Test Chamber operates by subjecting the connector housing to high-temperature, high-pressure water jets. This simulates extreme conditions that the component might encounter during actual use. The primary goal of this test is to verify that the connector housing can maintain its functionality under various climatic and environmental stresses.
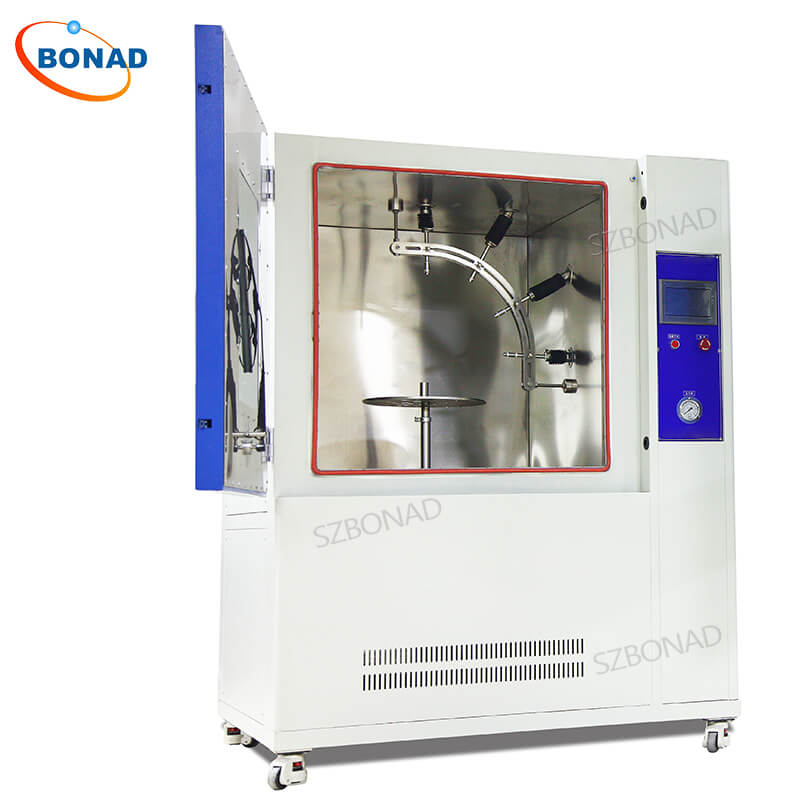
Components of the IPX9K Test Chamber
Conducting an IPX9K test requires specialized equipment, which includes:
- Water Spray System: Generates high-pressure, high-temperature water jets.
- Heating System: Elevates the water temperature to required levels.
- Pressure Control System: Maintains consistent water pressure throughout the test.
- Test Chamber: Provides an enclosed environment for thorough testing of the connector housing.
Steps in Conducting an IPX9K Test
- Securely mount the connector housing on the test bench.
- Set the temperature and humidity inside the chamber to specified values.
- Activate the water spray system, adjusting pressure and temperature as per test parameters.
- Expose the connector housing to water jets and monitor its performance.
- Continue spraying for a predetermined duration.
- Deactivate the spray system and normalize chamber conditions.
- Remove and inspect the connector housing for any damage or performance issues.
- Analyze data to assess waterproof capabilities.
Standards for IPX9K Testing
The IPX9K testing adheres to international protection rating standards (IP code), ensuring that connector housings can withstand high-temperature and high-pressure water jets without sustaining damage. Key standards include:
- Water Pressure: Must remain stable and sufficiently high to mimic severe conditions.
- Water Temperature: Should reach specified levels, typically elevated to simulate hot climates.
- Spray Angle: Must cover all surfaces of the connector housing for comprehensive testing.
- Test Duration: Should be long enough to observe performance under extended exposure.
- Result Evaluation: Post-test inspection should confirm that the connector meets waterproof and dustproof standards and functions correctly in real-world conditions.
By adhering to these rigorous testing protocols, automotive manufacturers can ensure their electronic components are robust enough to handle harsh environments, thereby enhancing vehicle reliability and safety.