To achieve the desired testing conditions, environmental test chambers must inevitably perform humidification and dehumidification operations. This article aims to analyze the various methods currently widely used in humid heat test chambers, highlighting their respective advantages and disadvantages, as well as suggesting suitable conditions for their use.
There are many ways to express humidity. For testing equipment, relative humidity is typically used to describe humidity. Relative humidity is defined as the ratio of the partial pressure of water vapor in the air to the saturation vapor pressure of water at that temperature, expressed as a percentage. From the properties of water vapor saturation pressure, it is known that the saturation pressure of water vapor is only a function of temperature and is independent of the air pressure where the water vapor may be located. Through extensive experiments and data organization, a relationship between water vapor saturation pressure and temperature has been established, with the Goff-Gratch formula being widely adopted in engineering and metrology.
The process of humidification essentially involves increasing the partial pressure of water vapor. The earliest method of humidification involved spraying water onto the walls of the test chamber and controlling the water temperature to manage surface saturation pressure. This method was introduced in the 1950s. However, due to poor adaptability in controlling large-lag hot water tank temperatures using simple on-off regulation with mercury contact conductivity meters, this method had a long transition period and could not meet the high humidification demands required for alternating humid heat tests. Additionally, spraying water on test samples caused contamination, leading to its replacement by steam humidification and shallow water pan humidification methods.
As constant humid heat tests evolved into alternating humid heat tests requiring faster humidification responses, steam humidification and shallow water pan methods became more prevalent.
The saturation pressure of water vapor increases with rising water temperature. When heated to boiling point under standard atmospheric pressure, a special steam boiler can quickly introduce steam into the test chamber for rapid humidification. However, since steam temperature often exceeds test condition requirements, mixing high-humidity steam with lower humidity air can cause condensation, releasing latent heat and generating extra heat within the chamber. To balance this additional heat, refrigeration might be needed which can lead to frosting on evaporators if not controlled properly. This necessitates increased humidification to maintain conditions but also introduces more heat into the system.
Steam humidification is widely used due to its fast response time suitable for alternating humid heat tests despite introducing extra heat into the chamber.
Shallow water pan humidifiers combine advantages from both steam and spray methods by using a sufficiently large surface area pan with heaters placed inside it. Water vapor diffuses into air without overheating but heating limitations make achieving low humidity challenging. Reducing pan water temperature through refrigeration can help lower humidity but requires draining pans during low-temperature tests or prolonged inactivity periods to prevent microbial growth.
With evolving testing requirements involving electrically active samples generating significant heat necessitating compressor cooling during tests – leading to moisture removal by evaporators – subcooled steam methods like ultrasonic or high-pressure misting efficiently convert micron-sized droplets into vapor absorbing sample-generated heat without adding extra system heat.
Two primary dehumidification methods are widely used: refrigeration dehumidification where moisture condenses on cooling coils forming frost (requiring control above 0°C) meeting most current test standards; and solid desiccant dehumidifiers capable of achieving very low dew points down to -70°C for specialized applications though expensive requiring continuous operation rotary desiccant units ideal for specific low-temperature engine testing scenarios demanding fresh air supply without excessive evaporator frosting impacting cooling efficiency.
In summary:
- Steam Humidification: Fast response but adds extra system heat.
- Shallow Water Pan Humidifiers: Effective without overheating but limited by surface area.
- Subcooled Steam: Efficient for high-heat sample scenarios without adding system heat.
- Refrigeration Dehumidification: Commonly used meeting most standards.
- Solid Desiccant Dehumidifiers: Specialized applications requiring very low dew points.
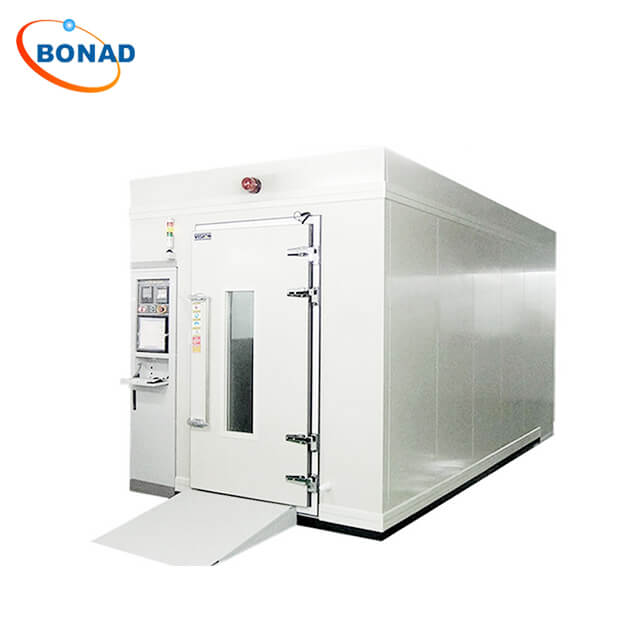